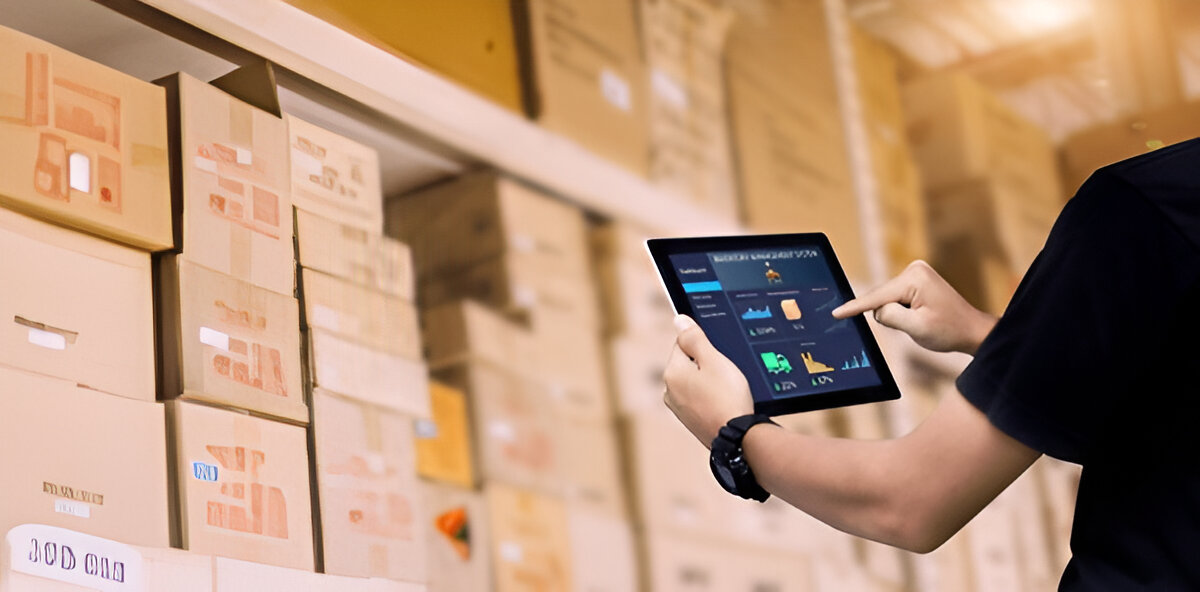
Warehouse Inventory System | How to Improve
23 January, 2025
Share to
Managing warehouse inventory has become increasingly crucial in today’s business landscape. The global warehouse and storage market was valued at approximately USD 1.01 trillion in 2023 and is projected to grow at a CAGR of 7.5% from 2023 to 2030, highlighting the mounting pressure on businesses to optimize operations. With the rise of e-commerce and increasingly complex supply chains, inventory tracking has become more challenging than ever.
This guide explores practical ways to improve your warehouse inventory system and maintain optimal stock levels for better business performance.
Essential Elements of Warehouse Inventory Management
An efficient warehouse relies on several key, well-coordinated parts. Optimizing these elements helps businesses run better and be more profitable.
Inventory tracking
Install real-time monitoring systems to prevent stock shortages and reduce waste. This includes alerts for low stock, accurate location tracking, and constant inventory monitoring. Accurate stock counts help businesses optimize inventory and ensure product availability.
Order fulfillment
Streamline the processes for picking, packing, and shipping orders. This will meet customer delivery expectations. This means organizing picking routes, checking quality during packing, and keeping clear records.
Shipping coordination
Establish robust systems for timely delivery while ensuring compliance with trade regulations. This includes accurate shipping documentation and tracking systems. Collaborate with carriers to optimize delivery routes and costs.
Reporting and analytics
Utilize data-driven tools to identify operational inefficiencies and drive improvements. Key metrics include inventory turnover rates, order accuracy, shipping times, and storage use. These insights help managers make informed decisions about stock levels and resource allocation.
Warehouse optimization
Use a WMS to optimize storage locations. It should base this on demand patterns and product characteristics. This includes analyzing seasonal trends, implementing dynamic storage solutions, and organizing inventory for efficient access.
Labor management
Ensure appropriate staffing levels to handle warehouse operations effectively. This includes training programs, tracking productivity, and fair pay. These help keep a skilled and motivated workforce.
Inventory control
Streamline processes for receiving, storing, and retrieving goods. This will cut handling time and reduce errors. This involves using standard procedures, automating where possible, and documenting all inventory movements.
How to Control Inventory Effectively
Effective warehouse inventory control requires a systematic approach combining technology, processes, and people. Here are the key strategies to implement:
Warehouse Management System Implementation
- Automated tracking: Deploy WMS software to monitor inventory levels and movements in real-time. It helps prevent stockouts and reduces counting errors. It also gives instant visibility into your inventory across all storage locations.
- Process automation: Streamline routine tasks like receiving, putaway, and picking through automated workflows. It reduces human error, speeds up work, and frees staff for complex tasks that need human judgment.
- Data integration: Connect inventory data across all business systems for better visibility. This keeps your e-commerce platform, accounting software, and warehouse systems updated with accurate information about stock levels and orders.
- Performance analytics: Track key metrics and generate reports for informed decision-making. Check indicators like inventory turnover and shipping times. They can find areas to improve and optimize operations.
- Mobile accessibility: Allow staff to use their mobile devices to check inventory information from any location in the warehouse. This removes the need for paper processes. It allows real-time updates to inventory records during picking and receiving.
Strategic Warehouse Inventory Management
- Regular monitoring: Establish systematic procedures for tracking stock levels throughout each day. This includes setting reorder points, safety stock levels, and regular cycle counts for accuracy.
- Optimization tools: They identify slow-moving items. Then, they optimize stock levels based on sales history and seasonal trends. Use ABC analysis to prioritize inventory. Focus on high-value items.
- Forecasting systems: Use data analytics to predict future inventory needs. They base this on historical data, market trends, and upcoming promotions. This helps prevent overstocking while ensuring enough inventory for expected demand.
- Lot tracking: Keep detailed records of product batches and end dates. This is crucial for perishable items or products with a short shelf life. This ensures proper rotation of stock and compliance with quality standards.
- Supplier coordination: Build strong relationships with suppliers to ensure reliable stock replenishment. Set clear channels for communication. Define lead times and expectations for order quantities and delivery schedules.
Warehouse Organization and Layout
- Logical arrangement: Organize products based on size, type, and movement frequency. Store fast-moving items near shipping areas for easy access. Group similar products to improve picking efficiency.
- Clear labeling: Use barcodes or QR codes for consistent product and location IDs. Clearly mark all storage locations, aisles, and zones to avoid confusion and errors.
- Automated navigation: Use technology to optimize picking routes and storage locations. This might include software that maps the warehouse. It suggests the best paths for order picking and restocking.
- Space optimization: Maximize storage efficiency while maintaining accessibility. Use vertical space with the right racking systems. Ensure aisles are wide enough for staff and equipment to move.
- Safety: Design the layout for safe handling and movement of the product. Have space between racks, clear exits, and areas for charging and maintaining equipment.
Best Practices Implementation
- Staff training: Educate team members on inventory control. Hold regular sessions to teach best practices and procedures. Include hands-on practice with equipment and systems, and provide updated documentation for reference.
- Regular audits: Conduct stock checks to ensure accuracy. This includes daily counts of some items and full inventory reviews at set times. Document discrepancies and investigate root causes.
- High-priority items: Focus on fast-moving, high-value products. Use extra security, count them more, and handle them specially.
- Quality control: Regularly inspect stored items. Check storage, packaging, and product quality. This includes monitoring temperature-sensitive items and checking for damage.
- Documentation: Keep clear records of all inventory moves and changes. This includes receiving records, transfer logs, and shipping docs. This creates an audit trail and helps track down discrepancies when they occur.
All these parts work together. They create a system that controls inventory. It improves efficiency and reduces errors.
Transform Your Warehouse: Your Path to Success
Improving your warehouse inventory system requires a balanced approach combining the right technology, well-trained staff, and efficient processes. Focus on systematically implementing these core strategies to achieve better inventory control, reduced costs, and improved customer satisfaction.
Connect with Cubework
Ready to transform your warehouse operations? Explore flexible, innovative solutions with Cubework. Call us at 888-599-7809 or email us at info@cubework.com to discover how we can support your business.